Rubber is a necessity for the production of gaskets, seals, tires, household products, shoes, industrial materials, fasteners and others. Natural rubber is soft and fragile, so the natural rubber used for further production needs to be vulcanized. Vulcanization is a process widely used in rubber industry. The vulcanization of natural rubber can thicken it and make it qualified for later production.
There is more or less a degree of ozone existed in the air. Even in ordinary air, ozone concentration there can be 0.01ppm. The strong oxidation of ozone makes it one of the best sterilization solutions. And more than that, it is also a great way to test the durability of certain materials. Some rubber products may be used in a variety of critical applications, so the requirements for rubber quality asks for an ozone resistance test. The wide use of rubber in various environments makes the ozone aging mechanism of rubber become the research direction paid attention to by both the manufacturers and users.

The action of ozone on rubber is often referred to as dry rotting, which includes cracking along the exposed, stretched or stressed face. There are over 10 kinds of rubber. The ones that are susceptible to ozone depletion and require ozone resistance test are as follows:
- Natural rubber
- Polybutadiene
- Styrene-butadiene rubber
- Nitrile rubber
The tolerance of a rubber material for ozone determines which applications it can be used in. For example, EPDM rubber is commonly used for making car door seals and weather stripping. It can keep stable in an ozone environment, so it can last a long time. To prevent deterioration during warehouse storage, rubber seals used in oil or fuel-related industries also require some ozone resistance. Ozone can attack rubber materials and cracks them. This calls for the attention to quality from the manufacturers. An ozone resistance test at different concentrations is an optimal test condition for rubber materials to be made into products.
In the experiment, the cracking of the rubber surface can be measured to assess the reliability of the material for specific applications. A controlled laboratory test according to industry standards for a certain rubber material can provide important reference information for rubber product manufacturers.

How to Do an Ozone Resistance Test
In an ozone resistance test for rubber, a sample will be placed in an enclosed ozone aging test chamber and exposed to a certain level of ozone concentration. The ozone concentration and duration are all set by a certain code or standard. Samples that cannot withstand a certain amount of ozone exposure will crack on the surface and even split in half. It is a routine test in the automobile and transportation industries. Other examples of elastomers that can be tested in the ozone chamber are polymers and silicones. When rubber is tested for ozone exposure, it is in contact with ozone gas in a closed space. Therefore, there is no need to worry about how to reduce and avoid any unpredicted exposure to ozone.
An ozone resistance test provides manufacturers of rubber products such as tires and many others with a test of the performance of their products over time. Such tests can also be used to ensure the quality of materials and components from new or suspected sources. Even a low level of ozone may cause damage to rubber materials. The acid content of rubber will increase over time with the exposure to ozone. There will be tiny cracks formed in the surface of rubber materials exposed to ozone.
Characteristic of Ozone Rubber Aging
When rubber is oxidized with its exposure to ozone, this reaction first occurs at the surface layer. A film will be formed first, followed by the cracking of the film. Over time, the film will break and reveal new surfaces. In this way, ozone aging can go deeper until the entire structure is destroyed.
Ozone rubber aging is a reaction that occurs on the surface. It takes a certain amount of stress or strain to cause the cracking of rubber. For unstretched rubber, a frost-like grey-white hard brittle film will be formed on the surface due to ozone aging. Ozone cracking occurs on films due to stress and strain. Its direction is perpendicular to the direction in which the rubber is stressed.
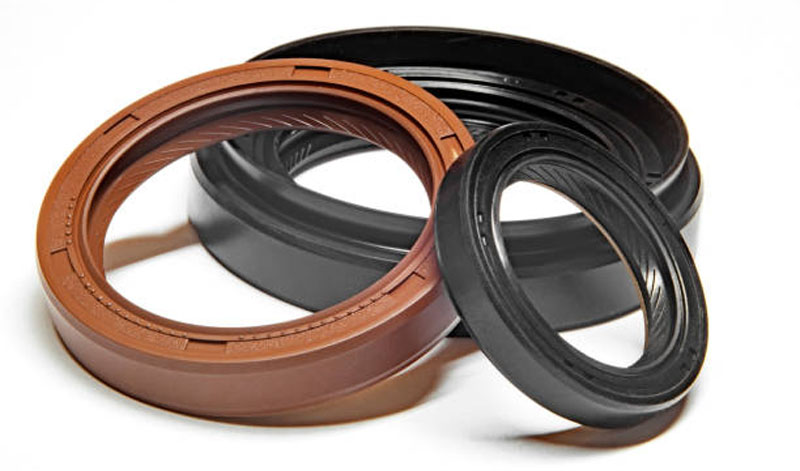
What will Affects Ozone Aging of Rubber?
1. Rubber type
The content of double bond in a type of rubber will affect its tolerance to ozone.
When the double bond content increases, its ozone aging resistance will decrease. The electron withdrawing substituent can reduce the reactivity of the double bond and thus the reactivity of ozone. Electron donating substituent can increase the density of the electron cloud, thereby improving the reactivity of the double bounds. The order of CR, BR and NR according to ozone aging resistance is CR>BR>NR.
2. Ozone Concentration
When there is a higher concentration of ozone, the resistance of rubber to ozone aging will be decreased. Under a certain level of ozone concentration, there will be different ozone aging resistance in rubber materials with different internal structures. For NR, cracks may be produced soon, but its expansion is slow. But for SBR, BR and NBR, it takes longer time to crack, but their expansion are faster.
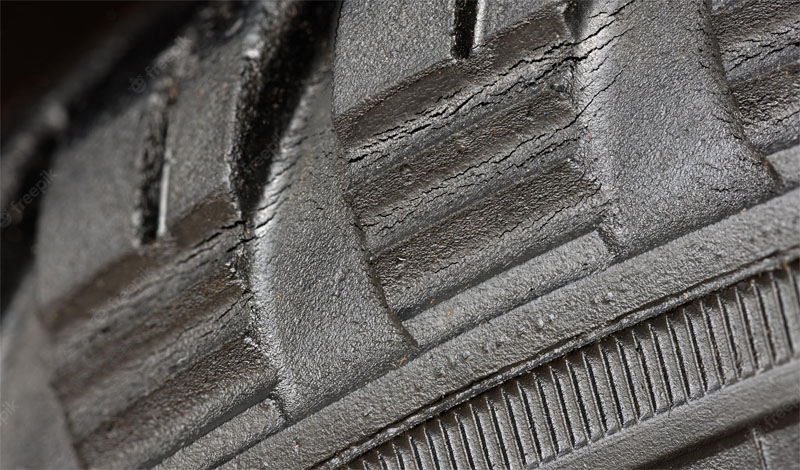
3. Stress and Strain
For the exposure to ozone, rubber materials will age and there will be ozonated films formed on the surface. These films are hard and brittle. They can prevent the ozone penetration into the interior. Under a dynamic condition, these films will be prone to breakage. Ozone will constantly react with rubber and finally cause the breaking. For rubber products with a lower elongation, there will be less cracks. But once formed, there will be a higher crack growth rate and deep cracks. For rubber materials with a higher elongation, there will be more cracks. But they develop relatively slowly, and most of them are shallow.
4. Temperature
The aging rate of rubber material is also proportional to ambient temperature. When the temperature rises, ozone rubber aging will also be accelerated.